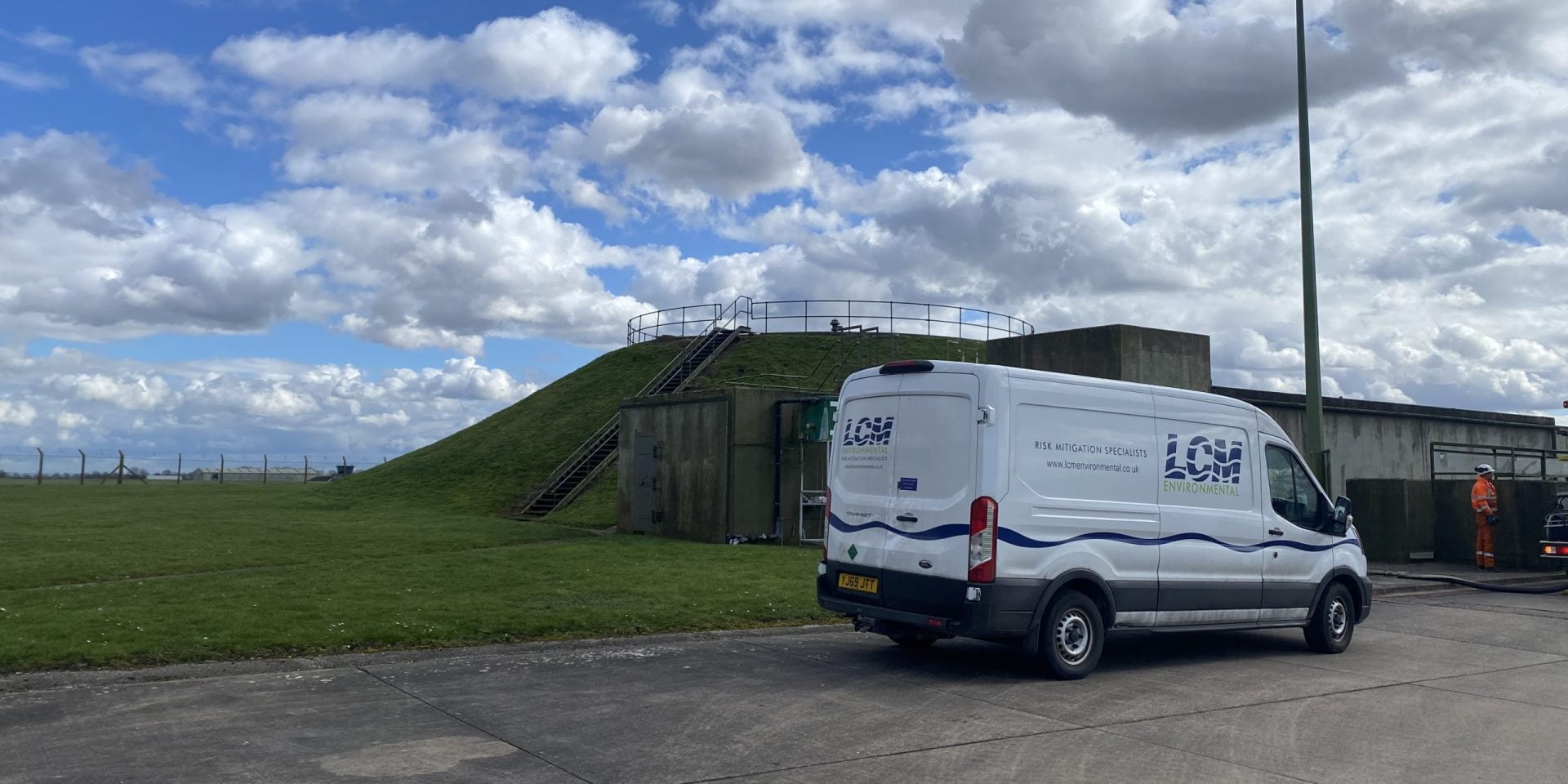
Defence Sector Case Study – Tank Cleaning and Fuel Asset Decommissioning
The Task
A multi-tank decommissioning programme of a BFI (Bulk Fuel Installation) was awarded to LCM from one of our defence customers. Work began on the military base in late spring, and the project has now been successfully completed.
The team carried out fuel uplifts from the various tanks and pipelines ahead of the industry clean, tank de-gas and certification. Phase two of the work was to remove all usable assets from the site. Once this was completed, the goods were palletised, wrapped and transferred to a local site for safe storage.
Scope of Works
On arrival, the LCM team collected their security passes which enabled them to travel around the base to the various work locations.
Ahead of the on-site meeting and job details being discussed, the engineers received their site-specific inductions, and task inductions and reviewed the health and safety paperwork. The LCM welfare unit arrived and was positioned in the designated area, the work area was segregated with heras fencing and safety signage. Once all paperwork was completed and the toolbox talks received, the engineers began scoping out the area and preparing for the following work, split into 5 stages.
Stage 1.
The removal and disposal of all fuel from the various vessels and pipelines. All fuel was taken off-site in LCM ADR Vac Tankers for disposal at a licensed facility.
Stage 2.
The draining and removal of the FWS (Fuel Water Separator) All internal elements were bagged up and removed from the site for disposal.
Stage 3.
Flushing and purging of all fuel lines were completed at various points along the pipelines to ensure that no ‘dead legs’ were missed, and no fuel remained within the system.
Stage 4.
Main bulk tank (1,250,000L capacity) for man entry cleaning. The tank was vented, and the lids were carefully removed. The cleaning process was carried out by a 7-person confined space and rescue entry crew and was performed to the highest standards of health and safety. Upon completion of the cleaning, the tank was dried and certified gas free.
Stage 5.
Non-man entry tank clean to the remaining tanks on site. 1 x 30,000L back-flush tank, 5,000L slops tank, 7,500L gas oil tank. All tanks were cleaned from the top and all washings were removed from site.
On completion of the cleaning tasks, salvageable assets were identified and removed for possible use across the military estate. Some of these included Hamworthy pumps, which were complete with motors and primer devices; ATEX lighting and switches, the FWS (Fuel Water Separator); all TRVs (Thermal Relief Valves) and DPIs (Differential pressure indicators) were salvageable, as well as two engine-driven generators, a dispense meter, slam shut valve and the entire control panel and tank gauging system.
The Outcome
After a several-week project, the client was left happy with LCM’s professional approach and quality work. All health and safety procedures were strictly followed and adhered to; no incidents were reported, and the engineers enjoyed a partial Red Arrows show to top up the experience.
Based on our client’s feedback, LCM is already working on further tenders for near-future MoD work in fuel infrastructure projects across the Defence Estate.