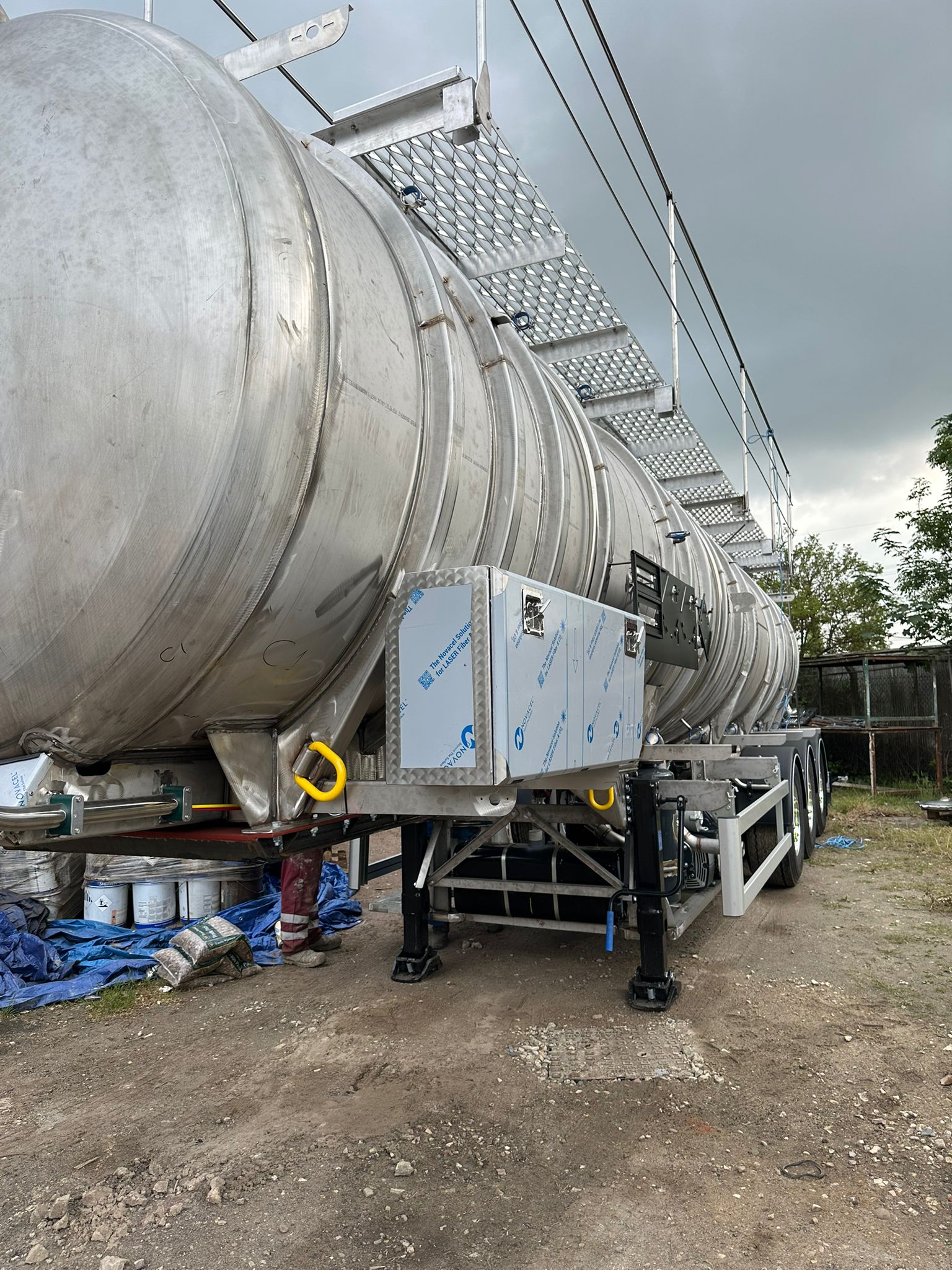
Road Acid Tanker Barrel Lining Case Study
The Task
Our client presented us with a critical task: to comprehensively restore the inside of a road tanker’s acid barrel back to specification.
The primary objective was to ensure its interior surfaces were thoroughly prepared and protected with a high-performance lining system. This was essential for extending the tanker’s lifespan, enhancing its operational safety, and maintaining its readiness for service.
The tanker arrived at our Kellington workshop, having been washed out, drained, and dried, with all pipework and fittings already removed.
Scope of Works:
Upon receiving the road tanker, our first step was to mask off all areas not requiring treatment, protecting components and ensuring the integrity of the surrounding structure.
We then proceeded with grit blasting the internal surfaces to achieve the stringent Swedish Standard SA2.5. This process, designed to create a minimum surface profile of 75 microns, is essential for optimal coating adhesion. Following this, we thoroughly removed all dust and debris, with responsible disposal handled by our team.
We employed a multi-layer coating system, with each component belonging to the same generic family. This ensures exceptional inter-coat adhesion, a critical factor in the long-term performance of the coating.
We applied Sprayglass LP Primer to a dry film thickness (dft) of 20 to 25 microns. This serves as a vital holding and prefabrication primer, providing a base for subsequent layers.
Following this, multiple coats of Sprayglass SG-459 glass flake coating were applied to achieve a nominal dft of 1.75 mm (with a minimum of 1.5 mm). This layer is key to the coating’s structural integrity and resistance. The Sprayglass SG-459 lining system is a multi-component medium-duty glass flake reinforced coating applied by airless spray, brush, or roller. It is formulated from a Novolac Epoxy Vinyl Ester resin and normally applied to give a dry film thickness of 1 – 1.25 mm.
We completed the coating process with Sprayglass Topcoat, applied to a dft of 200 to 250 microns. This topcoat significantly accelerates the full cure, maximises chemical resistance, and enhances both the surface finish and cosmetic appearance of the tanker’s interior.
We made sure the coating was impeccable by using several quality control steps. Our team applied extra coats to all welds and sharp corners, making these areas stronger. The coating was also carefully applied to all nozzle connections and flange faces, ensuring a smooth and consistent finish. To help our team, we used different coloured layers, which made sure the entire surface was evenly covered. We continuously checked the thickness of the coating as we worked using a special tool. Finally, we performed a full thickness check and a spark test to guarantee the coating was complete and working perfectly.
Outcomes:
The thorough execution of this scope of work resulted in a road tanker with an exceptionally durable and chemically resistant internal lining. By adhering to the highest industry standards for surface preparation and applying our advanced Sprayglass coating system, we successfully transformed the acid tanker barrel, readying it for the demanding operational environment it will face.
Our client received a tanker that not only met but exceeded expectations, providing long-term reliability and peace of mind.
To get in touch with our Coatings and Linings team, contact us at:
📞 0808 164 4570
✉ hello@lcmenvironmental.com